The Science Behind Porosity: A Comprehensive Overview for Welders and Fabricators
Understanding the elaborate mechanisms behind porosity in welding is essential for welders and makers pursuing flawless workmanship. As metalworkers dig right into the depths of this phenomenon, they discover a world regulated by various elements that influence the formation of these small gaps within welds. From the composition of the base products to the ins and outs of the welding process itself, a plethora of variables conspire to either aggravate or minimize the existence of porosity. In this thorough guide, we will unwind the science behind porosity, discovering its results on weld quality and unveiling advanced strategies for its control. Join us on this trip via the microcosm of welding imperfections, where accuracy fulfills understanding in the quest of perfect welds.
Comprehending Porosity in Welding
FIRST SENTENCE:
Exam of porosity in welding exposes critical understandings into the honesty and high quality of the weld joint. Porosity, defined by the existence of tooth cavities or spaces within the weld steel, is an usual problem in welding processes. These spaces, otherwise properly resolved, can jeopardize the structural integrity and mechanical homes of the weld, leading to possible failures in the completed item.

To identify and quantify porosity, non-destructive testing methods such as ultrasonic testing or X-ray assessment are often employed. These strategies allow for the identification of internal defects without endangering the stability of the weld. By examining the dimension, shape, and circulation of porosity within a weld, welders can make educated choices to boost their welding procedures and attain sounder weld joints.
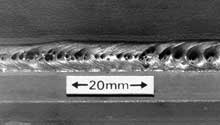
Variables Influencing Porosity Development
The occurrence of porosity in welding is influenced by a myriad of aspects, ranging from gas shielding efficiency to the details of welding criterion setups. One crucial element adding to porosity formation is insufficient gas protecting. When the shielding gas, usually argon or carbon dioxide, is not efficiently covering the weld pool, climatic gases like oxygen and nitrogen can contaminate the liquified metal, bring about porosity. In addition, the sanitation of the base products plays a significant function. Pollutants such as corrosion, oil, or moisture can vaporize during welding, developing gas pockets within the weld. Welding specifications, including voltage, current, travel rate, and electrode kind, additionally effect porosity development. Utilizing improper settings can generate too much spatter or warm input, which consequently can lead to porosity. The welding method employed, such as gas metal arc welding (GMAW) or secured steel arc welding (SMAW), can affect porosity development due to variants in heat distribution and gas insurance coverage. Understanding and controlling these variables are important for lessening porosity in welding procedures.
Effects of Porosity on Weld Quality
The existence of porosity also damages the weld's resistance to corrosion, as the entraped air or gases Homepage within the voids can respond with the surrounding atmosphere, leading to deterioration over time. Furthermore, porosity can impede the weld's ability to withstand pressure or impact, more threatening the general top quality and dependability of the welded framework. In essential applications such as aerospace, vehicle, or architectural buildings, where safety and sturdiness are extremely important, the destructive impacts of porosity on weld high quality can have severe consequences, highlighting the value of decreasing porosity with proper welding strategies and treatments.
Strategies to Lessen Porosity
Furthermore, using the suitable welding parameters, such as the proper voltage, current, and travel speed, is important in avoiding porosity. Keeping a constant arc length and angle during welding likewise assists decrease the probability of porosity.

In addition, selecting the appropriate securing gas and preserving proper gas circulation rates are crucial in decreasing porosity. Making use of the suitable welding strategy, such as back-stepping or employing a weaving motion, can additionally help distribute warmth uniformly and minimize the opportunities of porosity formation. Ensuring appropriate air flow in the welding atmosphere to eliminate any type of prospective sources of contamination is vital for achieving porosity-free welds. By carrying out these techniques, welders can properly minimize porosity and generate high-quality bonded joints.
Advanced Solutions for Porosity Control
Executing advanced technologies and ingenious techniques plays a crucial function in accomplishing remarkable control over porosity in welding procedures. Furthermore, utilizing innovative welding methods such as pulsed MIG welding or changed atmosphere welding can likewise assist mitigate porosity issues.
Another advanced service includes the use of innovative welding devices. Utilizing tools with integrated functions like waveform control and sophisticated power sources can boost weld top quality and minimize porosity threats. Additionally, the application read the full info here of automated welding systems with precise control over parameters can dramatically decrease porosity issues.
In addition, including sophisticated tracking and inspection technologies such as real-time X-ray imaging or automated ultrasonic testing can assist in finding porosity early in the welding procedure, enabling for prompt restorative activities. In general, incorporating these innovative solutions can greatly enhance porosity control and improve the total high quality of bonded elements.
Conclusion
In verdict, understanding you can find out more the scientific research behind porosity in welding is vital for welders and producers to generate high-grade welds - What is Porosity. Advanced remedies for porosity control can better improve the welding procedure and make sure a strong and dependable weld.
Comments on “What is Porosity in Welding: Secret Factors and Their Influence On Weld High Quality”